Pipework
Ewing Construction fabricates and installs fuel, chemical, gas, oil and process pipelines and carries out modification and maintenance work on existing installations. Ewing construction can offer full hydro testing and API 653 certification.
READY TO TALK?
Call us now +64 3 389 5999
Our purpose-build Hydraulic Jacking System enables us to complete the entire tank construction project working from ground level or below heights requiring permits. This eliminates suspended loads, making the process intrinsically safer. Less time and energy is expended accessing the work site and the time spent in confined space entry is reduced to the final strake.
The process requires an exceptionally small working footprint outside of the final tank diameter making building new tanks within existing facilities easier and safer to achieve.
Ewing Construction has successfully fabricated a wide range of tank designs with varying material compositions, from Horizontal Tanks, Vertical Tanks, Internal Floating Roofs and Fixed Truss Roofs, fabricated and tested to API 650. Materials used have ranged through a variety of grades of Carbon Steel, Stainless and Duplex Steels.
Ewing Construction has installed many underground piping systems that have included the project management of civil, mechanical, as well as instrumentation and electrical services on site.
Our strength is our ability to effectively plan and manage the integration of the various disciplines on site to achieve the best outcome for the client.
We take particular care with the installation of protective systems that may be required to give the client trouble free use of their asset for many years.
We specialise in complex installation environments associated with fluid delivery to tank farms and at airports for supply to hydrant lines.
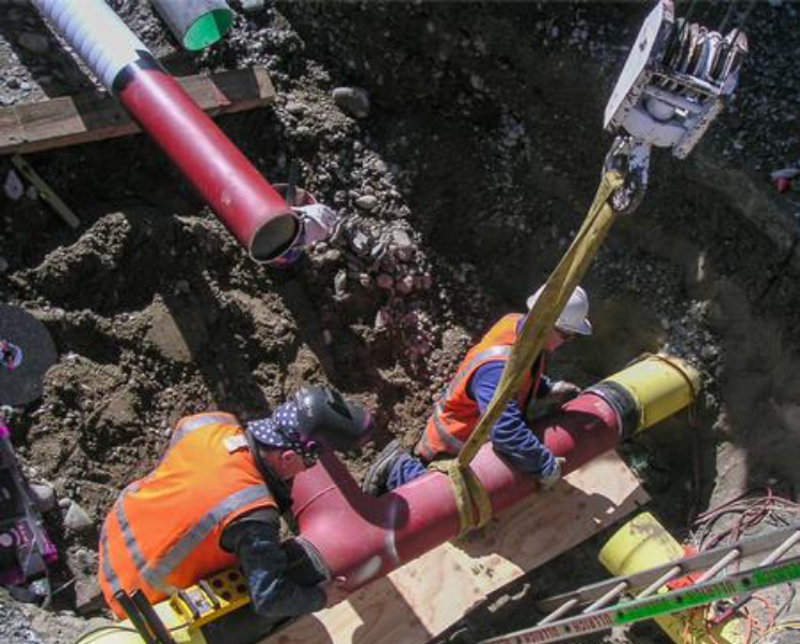
Marine Bunkering & Under-Wharf
Ewing Construction has installed fuel lines from storage terminals to the ships refuelling points.
These systems have varied in size from 50mm to 250mm travelling underground and above ground, and under the wharf out to the refuelling points.
Under-wharf construction is a hostile environment with extreme conditions, tides and shipping movements requiring superior HS&E systems combined with experienced operators to achieve a safe installation.
Over the years Ewing Construction has developed and refined systems to manage the challenges of installation and modification of wharf lines. Our comprehensive planning and preparation effectively manages environmental and safety factors on these projects. We have project managed and constructed multiple installations for over 20 years without any major incidents.
Ewing Construction also installs specified protective coatings required for these harsh environments.
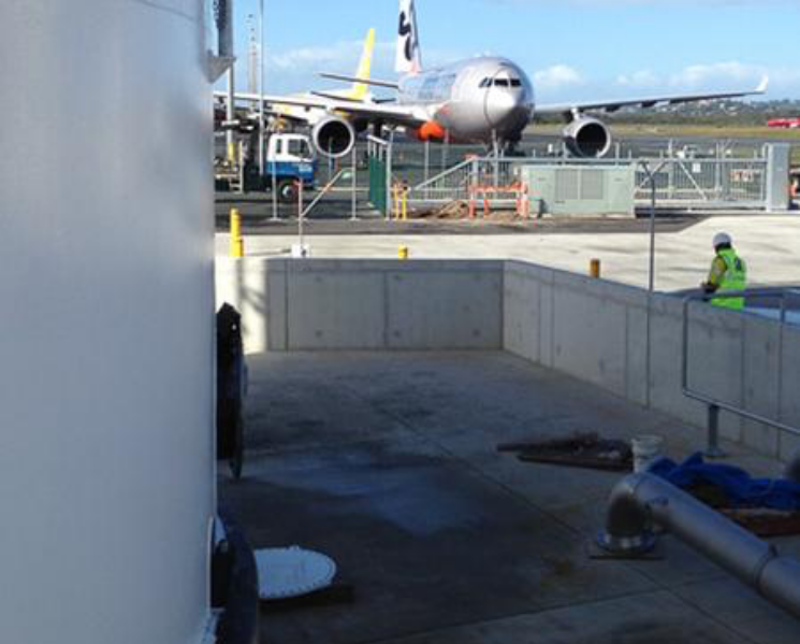
Aviation piping systems require extraordinary attention to detail to meet stringent specifications and dimensional accuracy.
Complex scheduling of works at operational airports is required when fabricating and installing Aviation Pipework at the fuel storage terminal and Airside.
Pipelines are often a considerable length and extremely challenging during the construction and installation phases. Working adjacent to fully operational aviation facilities also requires careful planning and execution, which Ewing Construction has consistently delivered for our clients.
Prior to installation the pipework has specialised coatings applied to protect the exterior from corrosion. Equally important is the application/installation of linings to protect the product from contamination. The internal coatings must be maintained at the highest standard to preserve the integrity of the fuel.
Ewing Construction has carried out many Airside Projects achieving the highest of standards under some of the most demanding conditions.
Ewing Construction has the necessary equipment and expertise to repair damaged or corroded sections of pipework.
Our experience and processes allow us to safely drain and contain product from existing pipework.
Often "Cold Cutting Equipment" is required to cut and remove contaminated sections of pipe. We fabricate the new work prior to installation.
Prior to returning to service we complete all testing and record results to enable final certification of the pipework.
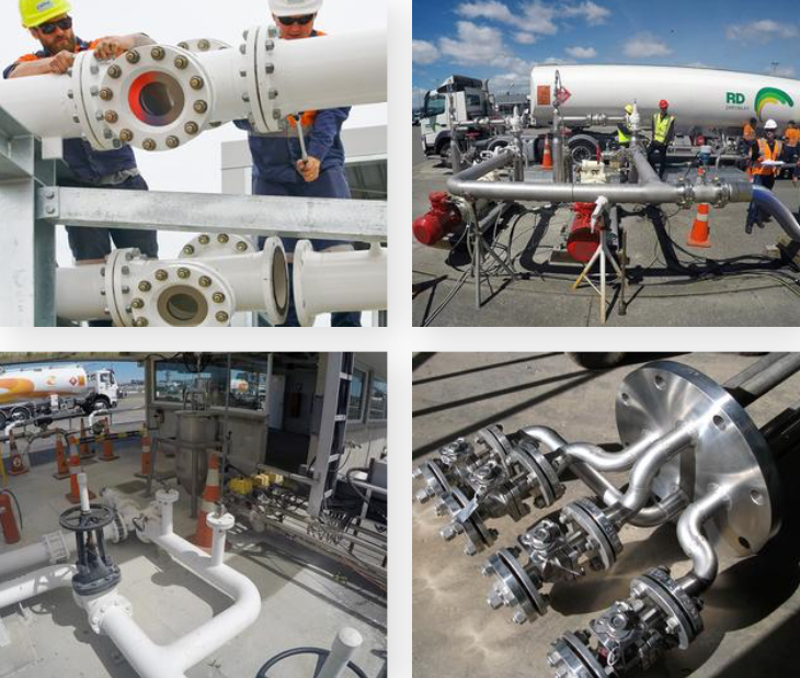